Industrial Gas Equipment: Gas Handling and Mixing
The industrial sector's lifeblood flows through a network of gases. Each of these gases needs careful management to ensure optimal performance and safety. Industrial gas equipment is reshaping manufacturing, healthcare, and research landscapes. Innovations are pushing boundaries, from cryogenics to hydrogen storage. Cryogenic systems now handle helium at -268.9°C, while storage solutions contain hydrogen at 700 bar. Industries can optimize processes and reduce risks by managing gases, equipment, and handling protocols.
Importance of Industrial Gases
These gases serve diverse functions, including creating controlled atmospheres for sensitive processes and supplying medical-grade oxygen. Precise handling and mixing of industrial gases is essential for several reasons:
- Product Quality: Maintaining gas purity and proper mixtures ensures consistent product outcomes.
- Worker Safety: Proper handling mitigates risks associated with high-pressure systems, asphyxiation, and reactivity.
- Process Optimization: Accurate gas management enhances efficiency in various industrial applications.
- Regulatory Compliance: Adherence to handling protocols ensures compliance with industry standards and regulations.
Industrial gas management demands technical equipment, strict safety protocols, and extensive training. This approach maximizes benefits and minimizes hazards.
Types of Industrial Gases DILO Handles
DILO specializes in handling a variety of industrial gases, each with unique properties and applications. Let's examine four key gases:
Helium (He)
Helium, a noble gas, has the lowest boiling point of any element at -268.9°C. Its applications include:
- Cryogenics: Cooling superconducting magnets in MRI machines and particle accelerators.
- Leak Detection: Identifying small leaks in vacuum systems or high-pressure vessels.
- Welding: Shielding gas for arc welding, especially for reactive metals like aluminum.
Safety: Helium is non-toxic and non-flammable, but can replace oxygen in confined spaces. Proper ventilation is needed when using large quantities.
Oxygen (O₂)
Oxygen is a reactive gas fundamental to many biological and industrial processes, and the use of specialized oxygen gas equipment ensures its safe delivery, storage, and monitoring . Key Applications:
- Medical: Supports patients with respiratory issues.
- Metallurgy: Enhances steelmaking efficiency.
- Wastewater Treatment: Accelerates organic contaminant breakdown.
Safety: While not flammable itself, oxygen supports combustion. Materials that don't burn in air may ignite in oxygen-rich environments. Strict handling protocols prevent fire hazards.
Xenon (Xe)
Xenon is a rare noble gas with specialized applications:
- Lighting: Used in high-intensity lamps for film projectors and specialized lighting.
- Space propulsion: Employed in ion engines for spacecraft.
- Medical imaging: Enhances CT scans for detailed lung ventilation images.
Safety: While non-toxic and chemically inert, xenon can cause asphyxiation in confined spaces by replacing oxygen. Its rarity makes it expensive, requiring careful handling to prevent waste.
Hydrogen (H₂)
As the lightest element, hydrogen helps with clean energy and industrial applications:
- Fuel Cells: Powers vehicles and backup systems, producing only water as a byproduct.
- Industrial Processes: Aids with petroleum refining and fertilizer production.
- Rocket Propulsion: Provides high-energy thrust for space launches.
Safety: Highly flammable and potentially explosive, hydrogen requires specific safe storage and handling equipment.
The properties and applications of these gases guide the choice of handling equipment and safety measures. DILO ensures safe, efficient, and reliable operations across industries.
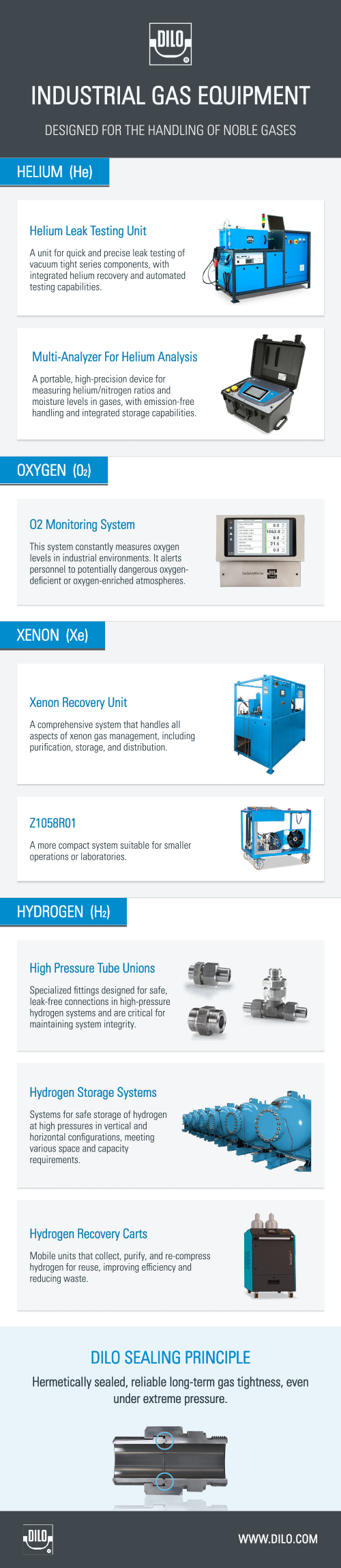
Industrial Gas Equipment
DILO provides a complete suite of industrial equipment designed to handle various industrial gases. Each piece of equipment is designed with safety, efficiency, and reliability, adhering to stringent industry standards. Let's explore types and their functions:
Helium Equipment:
- Helium Leak Testing Unit: This instrument detects tiny helium leaks in systems and components. It's for quality control in the aerospace, automotive, and electronics manufacturing industries.
- Helium Gas Handling, Storage, and Monitoring System: This integrated system manages helium throughout its use cycle. It includes storage tanks, purification units, and monitoring devices to ensure helium quality and minimize waste.
- Helium Compressors (B100R30, B100R40, B180R03): These compressors handle helium's unique properties. They maintain gas purity while compressing helium for storage or use in high-pressure applications.
- Multi-Analyzer for Helium: Provides high accuracy, zero-emission analysis of helium gas.
Oxygen Equipment:
- O2 Monitoring System: This system constantly measures oxygen levels in industrial environments. It alerts personnel to potentially dangerous oxygen-deficient or oxygen-enriched atmospheres.
- Gas Safety Room Monitor: Continuously detects leaks of up to seven (7) different gases including O2, CO, CO2, and C4.
Xenon Equipment:
- Xenon Recovery Unit: Given xenon's rarity and cost, it's vital to capture, purify and recycle xenon gas. This comprehensive system handles all aspects of xenon gas management, including purification, storage, and distribution. The xenon recovery unit is valuable in industries like aerospace, lighting and medical imaging
Hydrogen Equipment:
- Hydrogen Drying System: This system removes moisture from hydrogen gas to maintain purity in fuel cells and specific chemical processes.
- Hydrogen Recovery Carts: Mobile units collect, purify, and re-compress hydrogen for reuse, improving efficiency and reducing waste.
- Hydrogen High-Pressure Tube Unions: Specialized fittings are designed for safe, leak-free connections in high-pressure hydrogen systems and are critical for maintaining system integrity.
- Hydrogen Storage Systems: These systems safely store hydrogen at high pressures in vertical and horizontal configurations, meeting various space and capacity requirements.
- Electrolyzer: This device uses electricity to split water into hydrogen and oxygen, providing a clean method of hydrogen production.
- Hydrogen Filling Stations: Efficient systems that rapidly fuel hydrogen vehicles, accelerating the adoption of fuel cell technology.
What is Industrial Gas Handling and Gas Mixing?
Industrial gas handling contains the procedures, equipment, and safety protocols to manage gases throughout their lifecycle in industrial environments. This process begins with producing or procuring gases and extends through storage, transportation, use, and disposal or recycling.
Components of gas handling include:
- Storage: Using appropriate containers like high-pressure cylinders, cryogenic tanks, or bulk storage systems to maintain gas purity and prevent leaks.
- Transportation: Employing specialized vehicles and pipelines with safety features to move gases between locations while minimizing risk.
- Distribution: Implementing gas delivery systems within facilities, including piping networks, manifolds, and point-of-use outlets.
- Regulation: Using pressure regulators and flow controllers to manage gas pressure and flow rates for specific applications.
- Monitoring: Deploying gas detection systems and analytical instruments, such as the gas safety monitor, to ensure safety and maintain gas quality.
Gas mixing, a subset of gas handling, involves blending two or more gases to create specific mixtures. This process has uses in various industries and applications:
- Welding: Creating shielding gas mixtures to protect weld pools from atmospheric contamination.
- Calibration: Producing precise gas standards for calibrating analytical instruments.
- Atmosphere Control: Generating controlled environments for heat treatment or food packaging.
- Medical Applications: Formulating breathing gas mixtures for medical treatments or diving operations.
Advanced Gas Mixing Techniques
Research explores gas mixing at the microscale level. These insights promise more efficient and exact industrial processes, enhancing workplace safety through improved gas handling techniques. Proper implementation optimizes processes and reduces risks associated with gas management.
Safety Standards and Regulations in Gas Handling
OSHA Regulations for Gas Handling
The Occupational Safety and Health Administration sets clear gas handling standards for workplace safety. Key regulations include:
- 29 CFR 1910.101: General requirements for compressed gases.
- 29 CFR 1910.103: Specific standards for hydrogen.
These rules cover:
- Secure cylinder storage.
- Safe valve protection and transport.
- Handling protocols for hazardous gases.
- Gas detection and alarm system requirements.
Employers must maintain compliance through up-to-date safety programs and regular staff training.
Personal Protective Equipment (PPE) Requirements
PPE requirements vary based on the gas type:
- Cryogenic gases (e.g., liquid nitrogen): Insulated gloves and face shields
- Corrosive gases (e.g., chlorine): Chemical-resistant suits and specific respirators
- Flammable gases: Anti-static clothing and footwear
Proper PPE selection, use, and maintenance are critical for worker safety when handling gas cylinders or operating gas regulators. Regular training ensures the effective implementation of safety measures, whether working with natural gas or other industrial gases, including properly operating gas regulators.
What to Look for in an Industrial Gas Equipment Provider
When choosing an industrial gas equipment provider, focus on experience, safety record, and support. Seek companies with a proven record, excellent customer service, and skilled technical teams. Factors include:
- Industry expertise: Years of experience and knowledge of gas handling technologies.
- Product range and quality: Wide selection of high-quality, reliable equipment.
- Customization: Ability to tailor solutions to specific industry needs.
- Compliance: Adherence to OSHA and other relevant regulations.
- Support & Training: Ongoing customer service and training programs.
DILO exemplifies these qualities, offering gas-handling solutions across industries.
DILO's Services and Promise of Excellence
DILO leads the industrial gas equipment sector with products and services for efficient and safe gas handling. Our decades of experience and skilled engineering team allow us to provide innovative, tailored solutions for each industry's unique needs. From SF6 gas handling to advanced gas analyzers and monitoring systems, our equipment ensures precise control and safety in gas management. The SF6 gas filling and testing adapter kits and SF6 gas refilling devices exemplify our dedication to providing solutions for specialized gas handling needs.
When you choose DILO, you partner with a company committed to excellence in gas handling and mixing. Our expertise and continuous support ensure that your gas management processes are efficient, safe, and compliant with industry standards.
Contact us today to learn more about our industrial gas equipment and services.