Xenon Gas Equipment: Efficient Storage, Handling, and Industrial Applications
Xenon is a rare noble gas that commands high value in industrial applications due to its properties. Medical professionals use Xenon for imaging and anesthesia. Aerospace engineers use it for satellite propulsion.
As researchers find new uses for Xenon, manufacturers have made equipment to handle, store, and use this resource. This specialized gear ensures efficient xenon management. It also maintains strict purity and safety standards for its various uses.
Xenon gas equipment unlocks the element's potential across industries. Cryogenic storage systems preserve Xenon as a liquid. Precision flow controllers regulate its use in anesthesia. High-pressure compressors and specialized valves manage Xenon's unique properties in aerospace applications.
Recovery units recapture and purify used Xenon, slashing costs and minimizing waste. This equipment tackles Xenon's challenges, from its scarcity to its tendency to escape confinement.
This guide explores xenon gas equipment, covering:
- Applications across industries, from medical imaging to satellite propulsion.
- The handling challenges and innovative solutions in xenon gas management.
- Safety protocols and best practices in xenon handling and storage.
By understanding xenon handling and equipment, we can appreciate the systems that enable various applications.
Types of Xenon Gas Equipment
The xenon gas industry uses specialized equipment to manage this resource. Xenon gas handling requires expertise and precise tools to ensure safe and efficient use across various xenon gas applications.
Compressors
Xenon gas compressors are the workhorses of handling systems. These machines increase xenon gas pressure for storage or high-pressure applications.
Features include:
- Oil-free designs prevent contamination.
- Multi-stage compression achieves high pressures.
- Sealing technology prevents leaks.
- Cooling systems manage heat generated during compression.
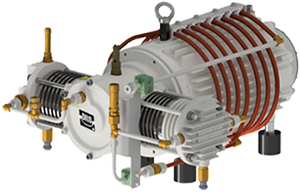
Storage Units
Storage units maintain xenon gas in its pure form. These units are high-pressure cylinders or tanks made from materials compatible with Xenon. This balance prevents reactions or contamination. Proper xenon gas storage maintains purity and prevents loss.
Aspects include:
- High-pressure resistance, often up to 300 bar or more.
- Specialized valve systems for safe filling and discharge.
- Vacuum-jacketed designs for cryogenic storage of liquid Xenon.
- Corrosion-resistant materials to maintain purity.
Safety Apparatus
Safety equipment is central when handling xenon gas. This category includes devices designed to protect personnel and maintain system integrity. Xenon gas safety is a top priority in all operations.
- Gas detectors: These devices track the environment for xenon leaks. They often use infrared or thermal conductivity sensors for high sensitivity.
- Pressure relief valves: These valves release excess pressure to prevent over-pressurization.
- Personal protective equipment (PPE): Specialized gear protects workers from potential exposure. This includes oxygen-deficiency monitors for personnel working in enclosed spaces.
- Emergency shutdown systems: Systems that rapidly shut down xenon equipment in emergencies.
Purification Systems
Xenon purification systems remove impurities to achieve high purity for various uses. They are central in industrial gas equipment and use several processes to keep Xenon pure. Common methods include:
Cryogenic distillation: This extraction exploits differences in boiling points to separate Xenon from contaminants.
Adsorption: Uses materials like activated charcoal or molecular sieves to capture impurities.
Catalytic purification: Removes specific contaminants through chemical reactions.
Membrane separation: Uses selective permeability to isolate pure Xenon.
Xenon Recovery Units
Given the rarity and cost, xenon recovery units capture and recycle used xenon gas. DILO offers several models designed for efficient xenon recovery.
Z820R01: This large-scale unit is for industrial xenon recovery operations. It features:
- Automated processes for efficient operation.
- High recovery rates can recover xenon gas down to low pressures.
- Integrated purification systems to ensure recovered Xenon meets purity standards.
- Control systems for precise operation and monitoring.
Z1058R01: A more compact system suitable for smaller operations or laboratories. Key features include:
- Ability to recover xenon gas down to pressures below 50 mbar.
- Portable design for flexible deployment.
- User-friendly interface for easy operation.
- Integrated safety systems to prevent gas loss.
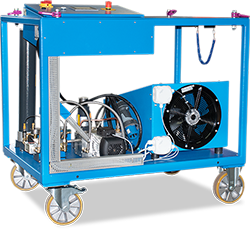
MINI Xenon Recovery Unit: This portable unit is for field operations or smaller facilities. It offers:
- Compact, lightweight design for easy transportation.
- Simplified operation for non-specialist users.
- Robust construction for reliability in various environments.
- Cost-effective solution for smaller-scale xenon recovery.
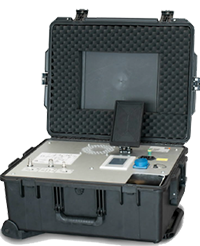
These recovery units have particle filters and dryers to verify that the recovered Xenon meets purity standards for reuse.
Gas Analyzers
Xenon gas analyzers monitor the purity and composition of xenon gas. They ensure that the gas meets the required specifications for its intended application.
Technologies include:
- Mass spectrometry for precise compositional analysis.
- Gas chromatography for detecting and quantifying impurities.
- Optical emission spectroscopy for rapid purity checks.
- Thermal conductivity detectors for general purity assessment.
Delivery Systems
Precision delivery systems supply exact amounts of xenon gas. Think medical anesthesia and industrial processes. These systems include:
- High-precision flow controllers.
- Pressure regulators for consistent gas delivery.
- Mixing systems for creating precise gas mixtures.
- Automated dosing systems for repeatable delivery.
Safety Protocols for Handling Xenon Gas
Although non-toxic and non-flammable, Xenon requires careful handling due to its asphyxiant properties and high cost. Safety protocols include:
Proper Ventilation
Install exhaust systems in xenon storage and usage areas to keep safe oxygen levels. Equip spaces with oxygen sensors that trigger alarms if levels drop below 19.5%. Implement automated ventilation systems that activate upon detecting xenon leaks.
Leak Detection and Prevention
Conduct daily equipment checks using xenon-specific leak detectors. Use helium leak testing for microscopic leak identification. Select gas-tight fittings and xenon-compatible seals to prevent escapes. Perform weekly pressure decay tests to catch subtle leaks in closed systems.
Pressure Management
Install pressure relief valves and rupture discs rated for Xenon's specific properties. Calibrate pressure gauges monthly to ensure precision. Train all operators in xenon pressure dynamics and emergency protocols. Deploy dual pressure monitoring systems for critical xenon applications.
Personal Protective Equipment
Impact-resistant safety goggles are required when working with pressurized xenon-mandate cryogenic gloves rated to -108°C for liquid xenon handling. Equip personnel with personal oxygen monitors in confined spaces. Keep positive-pressure SCBAs readily accessible for emergency response.
Training and Education
Conduct monthly xenon safety workshops covering MSDS details and emergency scenarios. Provide hands-on training with xenon equipment, emphasizing proper operation and safety features—test staff regularly on xenon handling procedures and emergency responses.
Storage and Handling
Store xenon cylinders upright in cool, shaded, well-ventilated areas, securing them with chains. Use only xenon-specific regulators and fittings certified for high-purity applications. Label all xenon storage and handling areas with clear hazard warnings and handling instructions.
Waste Management
Implement a closed-loop xenon recovery system to capture and purify used gas. Establish clear procedures for disposing of xenon-contaminated materials through certified waste handlers. Maintain detailed logs of all xenon usage, recovery, and disposal for regulatory compliance.
Maintaining Xenon Gas Equipment
Regular maintenance ensures xenon gas equipment's safety, efficiency, and longevity. Follow these guidelines to keep your systems in top condition:
Inspect Equipment Daily
Technicians should examine all components for wear, corrosion, or damage—test safety systems, including alarms and shut-off valves, to confirm proper function. Ultrasonic inspection can detect internal wear in critical parts.
Test for Leaks
Conduct routine checks with xenon or helium leak detectors. Focus on connections, valves, and seals—common failure points. Document and fix all leaks immediately to prevent xenon loss.
Calibrate Instruments
Adjust pressure gauges, flow meters, and gas analyzers. This ensures accurate readings and precise xenon flow control. Follow manufacturer guidelines for calibration schedules and record all procedures.
Clean and Purge Systems
Use compatible agents to clean components as specified by manufacturers. Purge systems with nitrogen before and after xenon use to prevent contamination. Implement clean room protocols when handling sensitive equipment.
Replace Filters
Change filters in purification and recovery systems according to manufacturer recommendations. Monitor pressure drops and contamination levels to determine replacement timing. Use HEPA filters to maintain clean environments.
Maintain Compressors
Perform oil changes with xenon-compatible lubricants for oil-lubricated models. Inspect and replace seals routinely to prevent leaks. Check and service inlet and outlet valves to ensure proper operation.
Document All Activities
Keep detailed maintenance, checks, and repairs records: store equipment manuals and technical documents for easy access. Use a computerized system to track maintenance schedules and history.
Train Staff
Provide thorough training on xenon equipment and safety procedures. Offer refresher courses on new techniques and equipment. Encourage staff to get relevant certifications in gas handling and maintenance.
Schedule Downtime
Plan regular maintenance periods for thorough equipment checks and repairs. Coordinate schedules to cut operational disruptions. Use predictive maintenance to optimize downtime.
Stay Current with Technology
Keep informed about new xenon gas equipment and industry best practices. Plan strategic upgrades to maintain efficiency and safety standards. Analyze the costs and benefits of new equipment. Consider energy efficiency and xenon recovery rates.
Recent Advancements in Xenon Gas Equipment
New technologies improve xenon gas equipment for efficiency, safety, and cost. A key focus area is xenon separation and purification. Recent studies reveal that metal-organic frameworks (MOFs) excel as Xe-selective porous solids. This breakthrough could enhance xenon gas equipment by allowing better separation and purification.
Other advancements include:
- Improved cryogenic systems for xenon liquefaction and storage
- Advanced materials for leak-proof seals and high-pressure containment
- Smart sensors and IoT integration for real-time monitoring
- Compact, portable xenon recovery systems for field use
Xenon gas equipment enables diverse applications, from spacecraft propulsion to medical imaging. Growing demand demands efficient, safe handling solutions. DILO's recovery units exemplify the industry's commitment to sustainability and cost value.
Strict safety protocols and maintenance maximize Xenon's benefits while minimizing risks. Ongoing research, like metal-organic frameworks for separation, promises to reshape xenon handling and unlock new uses.
Understanding xenon gas equipment is crucial for researchers, medical professionals, and engineers. Partnering with experienced providers ensures access to tailored solutions and expert support. As Xenon's potential expands, specialized equipment will continue to drive innovation across all industries.
For more on xenon gas equipment or to discuss your specific needs, contact DILO's experts. Our team can provide tailored solutions and in-depth guidance on xenon handling technologies.