1. Always Check Gas Quality Before Beginning Any Gas Handling
By-products of SF6are hazardous to human health and can damage gas handling equipment -if proper equipment pre-filters are not used. . Thus, checking SF6 gas quality before performing any maintenance is critical. Your technicians should use an analyzer before any type of handling procedure, which can check SF6 volume percentage, moisture concentration, and arc-byproducts - without emissions. During any quality control activities, make sure technicians are wearing the appropriate PPE and following all safety guidelines.
1. Always Check Gas Quality Before Beginning Any Gas Handling
By-products of SF6are hazardous to human health and can damage gas handling equipment -if proper equipment pre-filters are not used. . Thus, checking SF6 gas quality before performing any maintenance is critical. Your technicians should use an analyzer before any type of handling procedure, which can check SF6 volume percentage, moisture concentration, and arc-byproducts - without emissions. During any quality control activities, make sure technicians are wearing the appropriate PPE and following all safety guidelines.
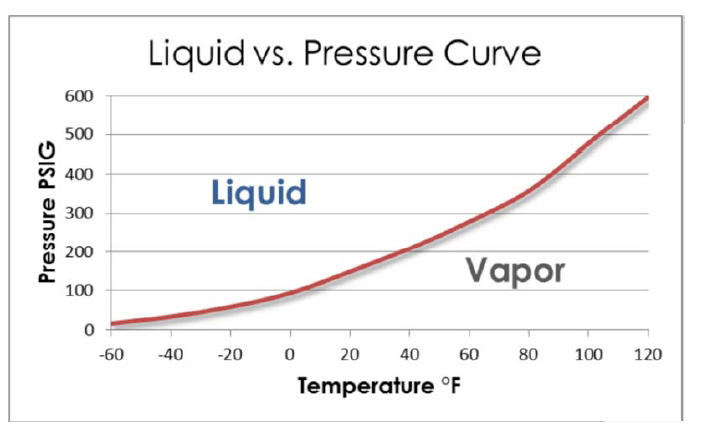
3. Recover to Blank-off Pressure
Recovery is the process of removing SF6 gas from gas-insulated equipment (GIE). A recovery system has onboard compressors to remove the SF6 gas while filtering out moisture and other contaminants.
If any residual gas is left in GIE, you risk harmful emissions. When using recovery equipment, the goal is to reach blank-off pressure: the lowest level of vacuum. This ensures that you’ve captured as much residual gas as possible. Minimum blank-off pressure levels are:
- <5 mbar (3.75 torr) for less than 100 lbs. of SF6 gas
- <1 mbar (0.75 torr) for greater than 100 lbs. of SF6 gas
To figure out the mass of SF6 gas, consult an SF6 density curve. Dividing the tank volume by density will determine the mass in pounds.
4. Utilize the Correct Size Recovery System
Another important consideration in SF6 gas recovery is the type of equipment you use. A Mini-Series service cart is convenient for small GIE. But if you try to use it with large volumes of SF6 gas, you’ll put stress on the equipment and you’ll spend much more time on recovery. A larger system can complete gas recovery in just a few hours while reaching the desired blank-off pressure.
Factor in hose length, as well: a longer hose might be a better fit in a larger facility, but it increases recovery time. DILO’s guide can help you choose a recovery system that can accommodate the volume of gas you are working with.
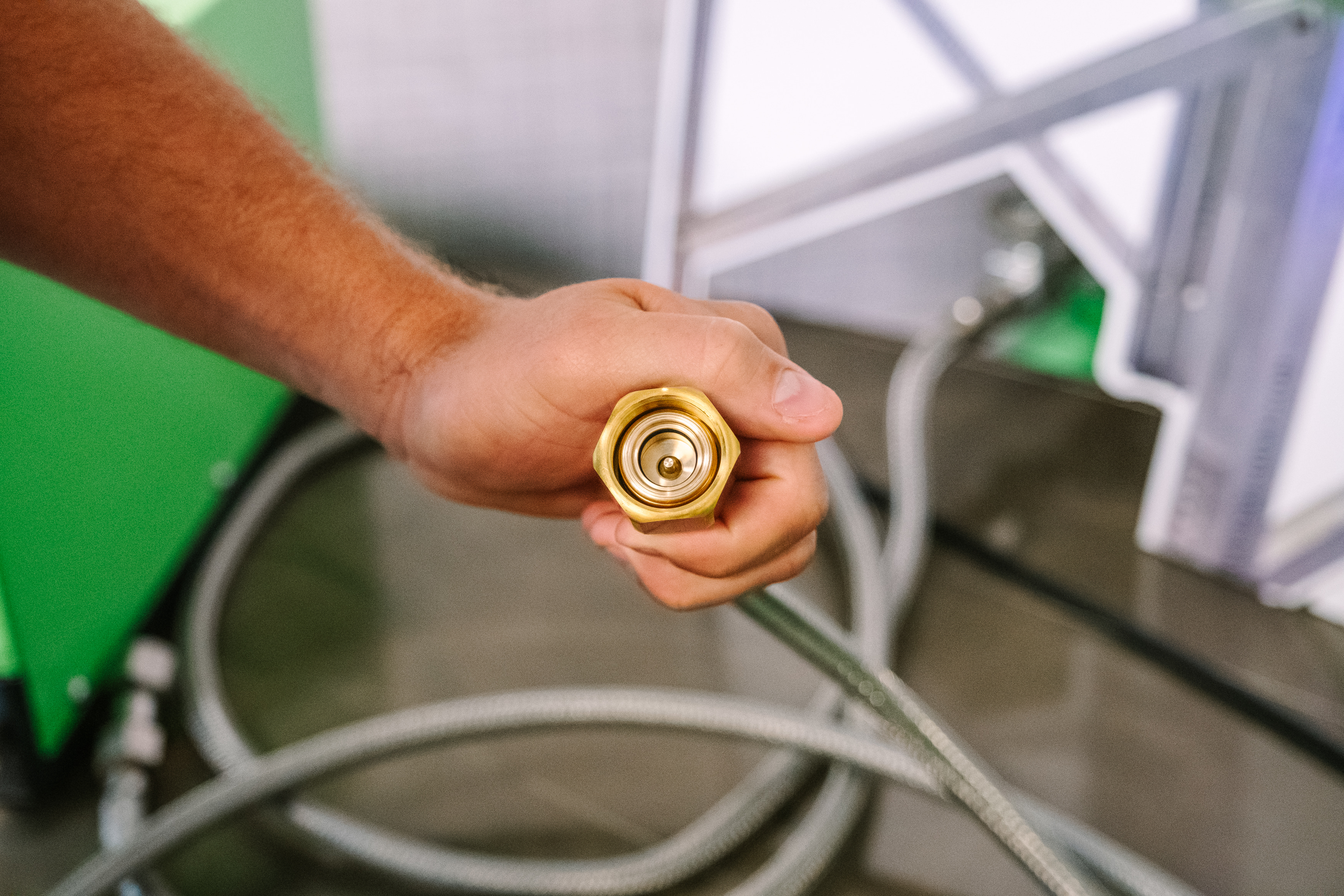
5. Remember to Cap Connections
This is a simple step that is often overlooked. To keep moisture, dust, and other debris out of SF6 gas equipment, you must cap the connections once maintenance work is complete. Most caps are made from plastic, aluminum, or stainless steel. Metal caps are usually best, as they have an O-ring that blocks moisture. Some caps come with a tether, which is a good option if you’re worried about misplacing a cap connection. DILO offers seminars to help you navigate capping connections.
Need More Information?
Well-trained technicians are the first line of defense against SF6 emissions. When it comes to operating SF6 gas handling equipment, even the smallest error can have costly and dangerous consequences. Knowing the proper protocols and safety procedures is key.
At DILO, we offer industrial gas equipment, as well as SF6 gas handling services. With a zero-emissions philosophy at the heart of everything we do, DILO provides virtual and in-person training on SF6 gas handling. We are proud to be an accredited provider through International Accreditors for Continuing Education and Training (IACET). IACET Continuing Education Credits (CEUs) are the industry standard for high-quality education and training.
With more than 50 years of experience in the industry, DILO provides comprehensive services for SF6 and alternative gasses combined with best-in-class customer care. We are headquartered in Odessa, Florida, and serve clients around the world. For more SF6 gas handling tips and training opportunities, check out DILO Academy today.